Forged this out of some 1 x 3/16" flat bar 1095 I had for knives. Left a nice as-forged finish on it except the teeth which I cut later. I've been planning on making one of these as I'm just not happy with the one I bought. Someone on the bladesmiths forum posted up a couple of his and they inspired me.
If you don't know, these are used on hidden tang knives. After you drill the holes in the block of wood to be your handle, you can use this to expand it until the tang will fit. A lot of people use them but not many people sell them. Most people end up making their own.
First pic is how it left the forge.
Then after I put the handle on. It's not perfect and I could still spend more time sanding scratches out of the handle but it is a tool...
If you don't know, these are used on hidden tang knives. After you drill the holes in the block of wood to be your handle, you can use this to expand it until the tang will fit. A lot of people use them but not many people sell them. Most people end up making their own.
First pic is how it left the forge.
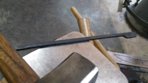
Then after I put the handle on. It's not perfect and I could still spend more time sanding scratches out of the handle but it is a tool...
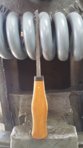
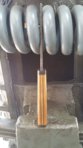